Electric cooperatives have a strong history of environmental stewardship. In fact, many electric cooperatives made commitments to the environment long before it was required by law.
Because co-ops are owned by the membership, the cooperative business model enables members to assert their voices to determine the direction of the co-op. Board directors elected by the membership also guide the cooperative to make decisions, establish policies and best practices, and carry out the vision of cooperative membership.
Basin Electric Power Cooperative, for example, was the first utility in the nation to require strip-mined land be returned to rolling countryside. This 1962 land reclamation policy came just a year after Basin Electric Power Cooperative incorporated in North Dakota and was written into its first coal contract. North Dakota’s first reclamation law wasn’t enacted until 1969.
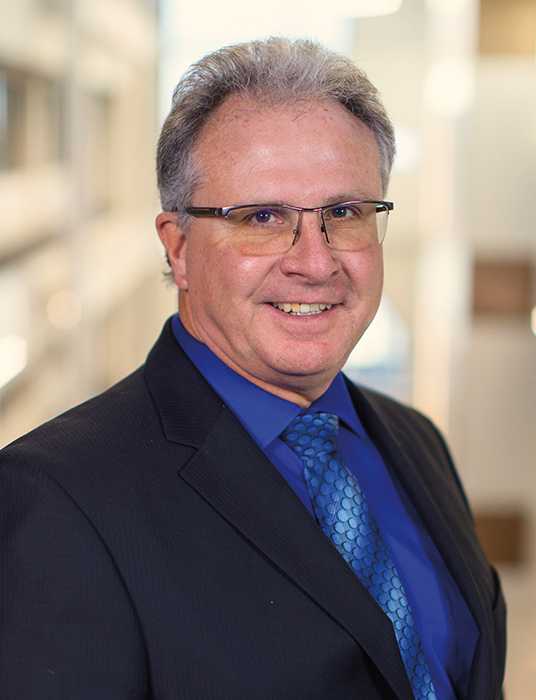
A concern for the environment, crafted and fostered by decades of member voices and decision-making, has been a present force since the creation of the electric co-op – and remains that way today. At the power generation and transmission level, three cooperatives with operations in North Dakota – Basin Electric Power Cooperative, Great River Energy and Minnkota Power Cooperative – demonstrate their environmental commitment through innovation and investment in large-scale projects, like the Wyoming Integrated Test Center, DryFining™ fuel enhancement process and Project Tundra.
INTEGRATED TEST CENTER
“My grandparents came across the prairie in a wagon to settle here,” says John Jacobs, senior vice president of operations for Basin Electric Power Cooperative (BEPC). “Why would we be punitive or want to scar the places that our kids, our families, our extended families have lived for decades?”
Jacobs has worked for BEPC for nearly 41 years. The engineer and Hazen native worked his way up through transmission, mining and plant operations and has seen the evolution of the coal conversation around carbon dioxide (CO2) emissions.
“Every time there was an issue with coal, it was industry that resolved that issue,” he says.
One example is the new Wyoming Integrated Test Center (ITC) at BEPC’s Dry Fork Station north of Gillette, Wyo. The ITC is a research test facility that provides space for research to test carbon capture, utilization and sequestration technologies using 20 megawatts of flue gas from Dry Fork Station. A major public-private partnership between the state of Wyoming, BEPC and several others, it enables real-world research and testing at an operational power plant.
“Can we take CO2 and make it into something else, into a sellable product for other companies to use?” Jacobs says.
Essentially, that’s the goal – to create a marketable byproduct with commercial value using CO2 emissions. How does it work? BEPC provides a zero-cost leased space at its Dry Fork Station, where five research teams conduct testing using the plant’s flue gas. Jacobs says the tenants start with 2 megawatts of flue gas and then scale up to the 20-megawatt mark.
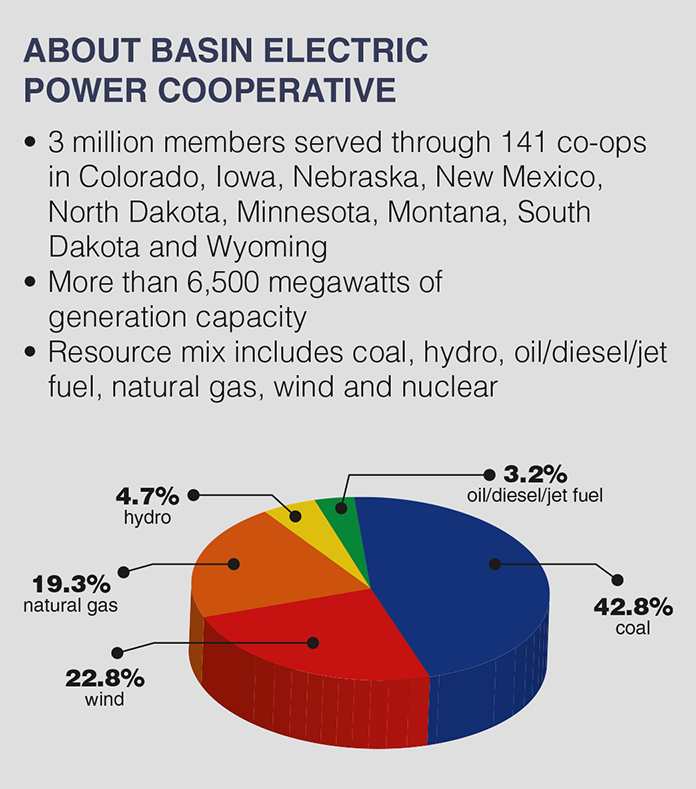
“Two megawatts is nothing compared to what emissions are worldwide,” he says. For perspective, the Dry Fork Station is a 385-megawatt facility. “They’re not trying to eat the whole elephant.”
Research teams, from India, China, Scotland, Canada and the United States, are ultimately competing for a $20 million NRG COSIA Carbon XPRIZE to develop these breakthrough carbon-utilization technologies. Some of the product ideas to be researched include bio-composite plastics, building materials and greener concrete.
Jacobs says XPRIZE provides monthly updates to BEPC. While the XPRIZE research space is currently unoccupied, BEPC is hopeful tenants will move in this year. Worldwide coronavirus concerns, however, may affect that timeline, Jacobs notes.
Additionally, a section of the ITC not affiliated with XPRIZE is currently being used by TDA Research (TDA). TDA moved equipment to Dry Fork Station in October 2019 and will test a novel hybrid carbon capture system, which incorporates membrane and solid sorbent technologies to remove carbon dioxide from flue gas.
“The ITC is a win-win for us,” Jacobs says. At a relatively low cost, BEPC can play a role in solving CO2 issues, while imagining a future for coal that protects the co-op’s legacy resources.
“Ultimately, we’re a co-op, which means we have to make the right decision for the guy at the end of the line with the meter,” Jacobs says. To do that with the current technology, Jacobs says coal has to be part of the equation. “Coal has gotten less and less of our portfolio. It’s still going to be part of an all-of-the-above energy situation.”
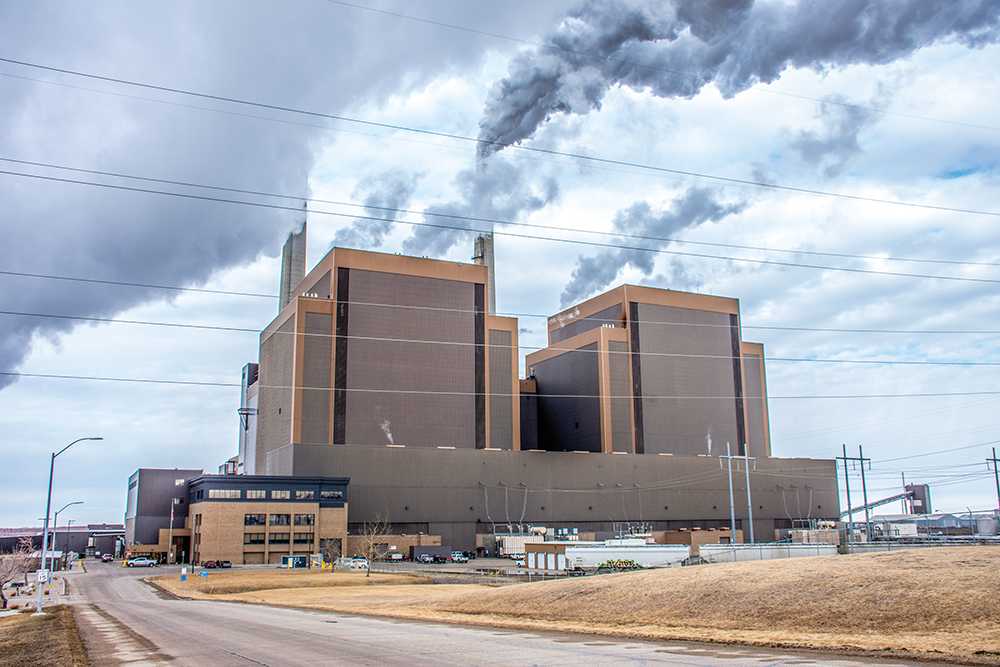
DRYFINING™ TECHNOLOGY
In the late 1990s, Great River Energy, which owns and operates the Coal Creek Station near Underwood, started experimenting with the lignite coal enhancement process. North Dakota lignite coal presented advantages at a mine-mouth location, but the higher moisture content in lignite meant Great River Energy had to burn a lot more coal to produce energy equivalent to that of other coal types.
“Our engineers conceived an idea of how we can utilize waste heat from the power plant to make the plant more efficient, and in doing so, we have fewer emissions, have lowered our CO2 output and the plant just runs better,” says David Farnsworth, Great River Energy’s manager of North Dakota power generation and engineering services and a North Dakota State University engineering grad.
With a 2003 U.S. Department of Energy (DOE) grant, Great River Energy pursued the research, under the agreement to commercialize any successful outcomes.
The process used waste heat from the plant to dry lignite coal through a thermal drying process, which raised the per-pound heating value of the coal from 6,200 to 7,100 Btu.
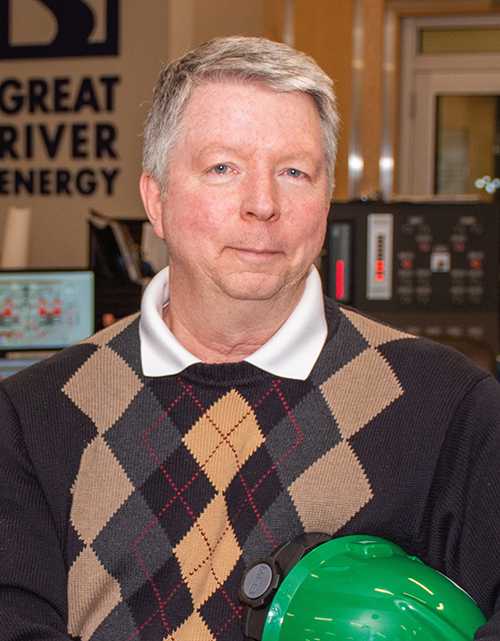
Only about 35 percent of the energy contained in power plant fuel gets converted into electricity and the rest goes out as heat, called residual or waste heat, Farnsworth explains. Waste heat is the steam one would see coming out of the stacks at a coal plant.
“We started out with a barrel of coal, then moved to a pile of coal,” Farnsworth says of the fuel-enhancement research phase. “Once we scaled everything up, we determined we could actually do some additional things to the coal to remove some of the bad actors in coal, like sulfur and mercury.”
By adding a mechanical segregation process, engineers were able to segregate the lignite stream and remove the higher-density compounds that contain higher levels of sulfur and mercury.
The resulting technology is known as the DryFining™ fuel enhancement process, which includes both the thermal drying and mechanical segregation of lignite coal.
“It’s been a great technology for us. We hold nine U.S. patents on this technology,” Farnsworth says. Plus, potential applications are possible both overseas and domestically.
As a result of the DryFining process at Coal Creek Station, plant efficiency has improved 4 percent and over $20 million is saved annually in operational and maintenance costs. Emissions have also been significantly reduced, including carbon dioxide emissions by 4 percent, sulfur dioxide emissions by more than 40 percent, nitrogen oxide emissions by more than 20 percent and up to 40 percent mercury emissions.
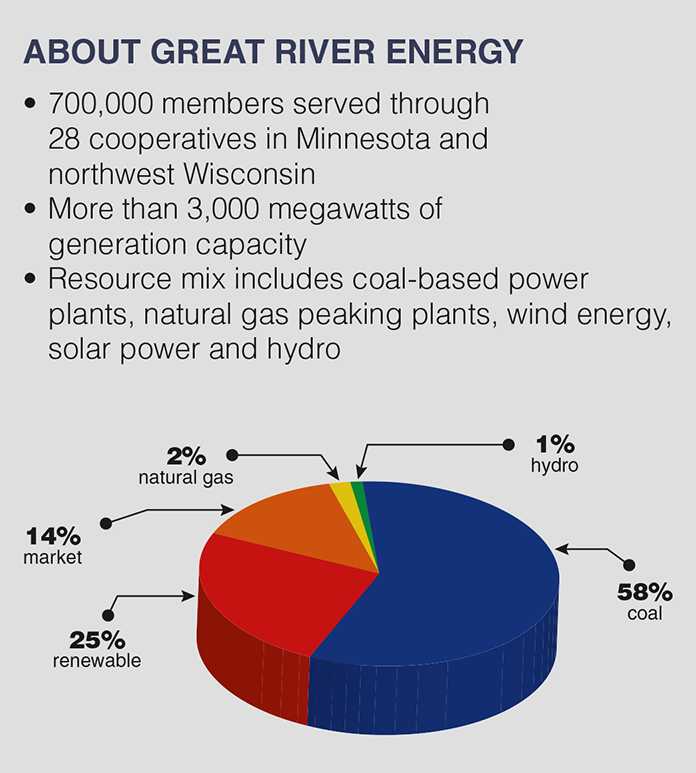
“If you can get a 2 percent efficiency gain, you’re doing well. We’ve gotten 4 percent,” Farnsworth says. “We are serial No. 1. This is state-of-the-art technology.”
What is the best part, if you ask Farnsworth?
“This is really a homegrown project,” he says. “It was all conceived and commercialized through engineers at this plant, who are all North Dakota-educated engineers.”
“I’m very proud of all the people who were involved. We have people who are very forward-thinking, very creative and very smart,” he says.
Farnsworth also credits GRE’s culture and the support of its board of member-owners for the DryFining technology success and constant move toward environmental improvement.
“The GRE culture of innovation and progressive technology allows us to have our ideas, and if they’re good ideas, our board will entertain those,” he says.
“Commitment to environmental stewardship is one of the three pillars of our business,” he says. “Even long before regulation was in place, we were scrubbing extra hard and being proactive in our environmental practices. I’m proud of our board of directors and senior management who trust us to do the right thing.”
.jpg)
PROJECT TUNDRA
In the middle of North Dakota’s backyard, Minnkota Power Cooperative (Minnkota) is working on a project that, if successful, would be the largest carbon capture and storage facility in the world. Aptly called Project Tundra, the goal is to build a carbon capture facility that would capture 90 percent of CO2 emissions from the Unit 2 generator of the Milton R. Young Station near Center, which Minnkota operates and partially owns. The captured CO2 would then be safely and permanently stored near the plant site in a geologic formation about a mile underground. If completed as planned, the project will remove 4 million tons of CO2 annually – the equivalent of taking 800,000 cars off the road.
“North Dakota is really ideally situated for a project like this, because our geology is so stable and uniquely suitable for geologic storage of CO2,” says Ben Fladhammer, communications manager for Minnkota.
Project Tundra began about five years ago and is modeled after the successful Petra Nova project in Texas, which proved these technologies can work at scale, says Dan Laudal, Minnkota’s environmental manager. Around the same time, the Clean Power Plan was dominating the national energy dialogue.
“We started looking at things to be able to maintain our existing assets in a carbon-managed future,” Laudal says. “I don’t think we know what that’s going to look like, but we’re trying to be proactive and mitigate that uncertainty.”
The research phase followed. Minnkota set to work characterizing the storage facility, utilizing the resources and expertise of the Energy and Environmental Research Center (EERC) at the University of North Dakota, looking at the capture systems and how they would perform on lignite flue gas and in a cold environment, and overall trying to design the systems to be functional for this application.
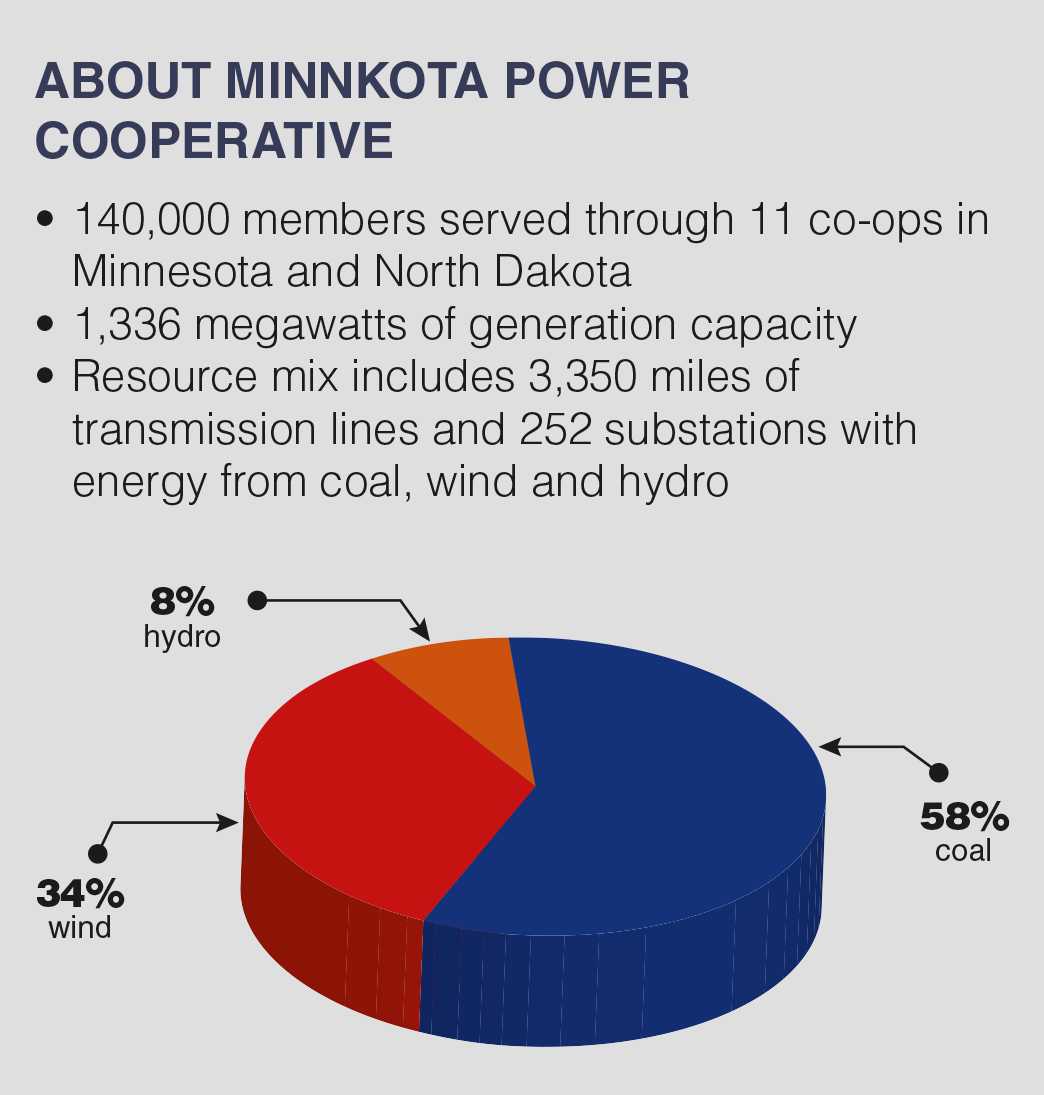
In early 2019, the focus of Project Tundra shifted from research to the commercial phase.
“We’re taking everything we’ve learned and transitioning that into commercial design, permitting activities and ultimately trying to be able to get it financed and built,” Laudal says. “We’re very confident that this can get done.”
Minnkota anticipates having all of the permitting submitted by the end of this year. If approval for those permits is received by the end of 2021, the co-op will be able to close on financing as early as 2022, at which point the building phase will commence. Minnkota says it will utilize the 45Q tax credit to finance the project, so member rates will be unaffected.
“Last winter’s polar vortex really demonstrated why we need to keep these (coal) assets up and running, and Project Tundra is an opportunity to be able to do that cost effectively,” Laudal says.
In reality, this project is much bigger than Minnkota or North Dakota alone. The success of Project Tundra will make waves in the industry – eyes are on North Dakota. Fladhammer says the project has already received national media attention from The New York Times and The Wall Street Journal.
“One of the things that’s important to us is the global picture, as well,” Laudal says. “CO2 is a global issue. If we can take the leadership role in North Dakota and the United States to bring costs down, and then ultimately sell the technologies we develop to other parts of the world that are expanding use of fossil fuels, it’s both an environmental and potential financial reward.”
Progressing efforts like Project Tundra, DryFining and the Integrated Test Center forward are no small feats. These projects demonstrate electric cooperatives’ lasting commitment to the environment and why the cooperative business model continues to light the path toward better environmental stewardship.
“As a co-op, we’re far more agile, just because we’re governed by our board, and we’re able to work very closely with them to make decisions and to move things forward,” Fladhammer says. “I think we have a longer-term view as a co-op.”
Cally Peterson is editor of North Dakota Living. She can be reached at cpeterson@ndarec.com.